Powering the Robotic Future
The world of manufacturing is changing. A hundred years ago, the energy powering a factory was, to a large degree, provided by the muscle power of its employees. Today, factories consume enormous amounts of electrical power. That power supplies the computers, automated equipment and robots that have made our factories so efficient. But electrical energy available is not limitless. So what is being done to make sure this energy is being used efficiently?
How efficient are electrical devices?
Factories need power to make the goods we buy and use every day. A lot of power. A small factory might use as much energy in a week as a household uses in a month. Larger ones can use that amount in a single day, or even a few hours. In order to ensure that the products we consume can stay affordable, every improvement in automation in factories, such as adding robots, has also required that those machines use electrical energy efficiently.
The electronics industry has been key in making this happen, specifically all the scientists and engineers who research, design and develop the components and their materials. To put into perspective how advanced today’s generation of home appliances are, we only need to look back to audio systems from the 1980s. Back then, the amplifiers in such a system were around 50 – 60% efficient. This meant, for every watt of output power, around half was being wasted. The energy lost was mostly released as heat which also applies to washing machines, fridges, freezers and televisions.
How does electronics help to make things more efficient?
There are two approaches to improving efficiency when it comes to electronics:
First approach: Components themselves
Over time, components have become smaller and more efficient. New materials also allow us to make components that can do more in smaller packaging than we could previously. All this research happens because customers are demanding that the components, the building blocks of electronic circuits, need to be more efficient.
Second approach: Strategies for using electronic components in electrical circuits
Back in the 1980’s, the approaches to building an amplifier were limited. To some degree this was due to the limits of the components. However, in others it was due to the huge cost involved in making a circuit that would only be marginally more efficient. The improvement in performance didn’t justify the cost.
But engineers knew that, if they had the appropriate electronic devices, they would be able to undertake extremely clever approaches that could result in very efficient electronics.
One further change is in the growth of digital technology. Years ago, something handling analog signals, like an amplifier, would be built purely using analog circuitry. Nowadays, powerful, compact and efficient amplifiers, combine the best of both analog and digital techniques. This is the case for televisions and surround-sound home cinema systems. The result: compact, powerful and efficient audio amplifiers for our home audio needs.
It’s all about the timing of the power delivery
Delivering power to electronic circuits is another demanding task. Power supplies are used to convert alternating current, the electricity we get from our wall sockets, into direct current, a form of electricity which our phones can use for charging and powering many other household gadgets, large and small. Sometimes, the appliance that is attached requires lots of power; other times, it needs very little. On occasion, it requires no power at all. Typically, providing a constant amount of power is a relatively simple task that can be performed efficiently. The challenges occur when the power demands change. The technical term for this is “a change in load”.
This is the challenge engineers take on when designing and building power supplies. It is a little like trying to solve a puzzle. Most times, there is an excellent solution for providing a small amount of power, while another solution is excellent at providing large amounts of power. However, making those circuits good, rather than mediocre, for the times when they are being pushed into their less efficient operating modes, is a real challenge.
Making decisions based upon insights
What most engineers would like to have is more information about the planned use cases for the electronics they are designing. When building a power supply that will be used in a factory to power a robot, they’d like to know how much power will be used and when. For example, when the robot picks something up, it will use a lot of power. Once the item has been set down again, it will consume very little. A robot arm that continuously has to move quickly will also use more energy than one that is moving slowly.
But a robot is a universal tool, capable of accomplishing many varied tasks. The energy used by the robot when lifting heavy car parts will be different to when it is used for making office furniture.
Wouldn’t it be great if all these energy consuming devices could communicate with one another to organize and optimize their energy consumption?
Industry 4.0: More power efficiency through machine-to-machine communication
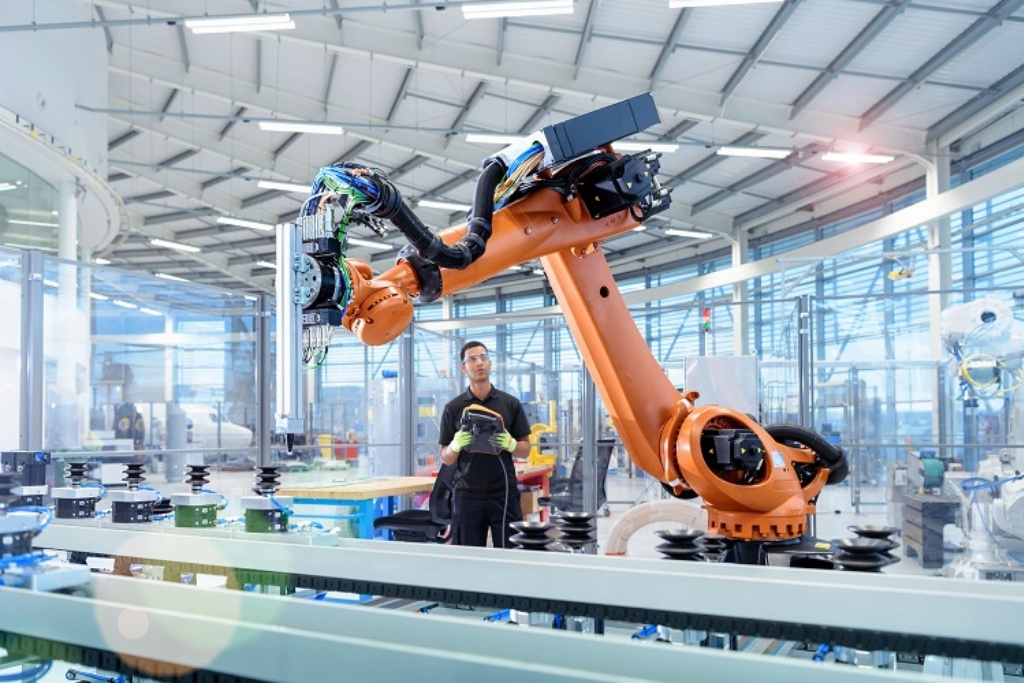
This is where initiatives such as Industry 4.0 come in. The term is broad in its definition but is typically understood to define the next age in the industrial revolution. This is the age of intercommunication, where robots and other manufacturing equipment talk to one another, as well as to their human operators, to achieve further efficiencies in how factories produce goods.
One area for efficiency improvements is in power consumption. If the machines could coordinate with one another, perhaps they could smooth out their energy usage and reduce the number of sudden changes in demand. This would result, as discussed earlier, in more efficient use of energy.
Obviously, this doesn’t work all the time. If a conveyor belt of materials needs to be picked up and placed into a box, there are timing constraints that must be fulfilled. However, if the machines were talking to one another, they could collectively find a more efficient order of operation that also results in a smoother power usage.
Infineon’s contribution to saving energy
Infineon delivers a large proportion of the electronic content for power supply electronics. Until recently, the overwhelming majority of those components have been based upon a base substrate of pure silicon. This is the material silicon chips are made of. However, advances in material science have discovered alternatives that are highly appropriate for use in power electronics. One that is gaining importance is silicon carbide, also known as SiC.
SiC has been around for a long time for use in electronics, but it is only in the last decade that it has been productized for use in power electronics. Its benefits include a high current density, making it ideal for the high voltages and currents of power supplies.
In an industry where every little counts, Infineon’s CoolSiCTM Schottky diodes are helping engineers improve efficiency in power supplies by another percentage point or two. This may not sound like much, but it is making the difference in an industry where efficiencies of more than 90% are now regularly being reached.
More efficiency also means less wasted energy that would otherwise have to be dissipated as heat. This results in designs that can be lighter and more compact, as well as also requiring less resources to draw that heat away (typically a copper cooling element and a fan).
So, by coupling such high efficiency components with Industry 4.0 machinery that talks to one another, the power supplies can achieve exceptionally high efficiencies, thereby reducing waste. At the same time, by knowing how the loads they are supplying are changing, as well as those of other machines around them, they are able to react and operate in the most appropriate and efficient mode.
Conclusion
We want to make sure that the factories of the future use our limited resources as efficiently as possible. Thanks to the collective efforts of scientists, we are learning more about the fantastic properties of materials that can make this happen. And, with the support of clever engineers, these materials and insights are being turned into the energy saving solutions and components that will make this happen.
Sounce: https://www.infineon.com/